

- #Solidworks flow simulation fan tutorial cracked
- #Solidworks flow simulation fan tutorial full version
- #Solidworks flow simulation fan tutorial serial number
- #Solidworks flow simulation fan tutorial .exe
- #Solidworks flow simulation fan tutorial update
Supports up to 3x 360 radiators and a maximum of 10 fans.
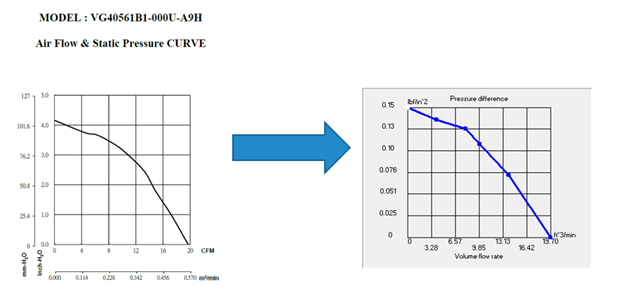
If merge modules are used, the Crystal Reports runtime is installed each time a deployment project is installed on the target computer. document will open with the Flow Simulation Tutorials. SOLIDWORKS Flow Simulation is a powerful, general-purpose CFD package integrated directly into. In this case, Crystal Reports runtime files are installed once. You can use the Windows Installer when many deployment projects are installed on the same target computer. msi file is used for installation on target machines, merge modules do not need to be added.
#Solidworks flow simulation fan tutorial .exe
exe setup file, merge modules are included in a deployment project because they install the Crystal Reports runtime. Based on this rigorous verification suite, SOLIDWORKS Flow Simulation offers 26 tutorial benchmark examples ready for immediate use. Before releasing a new version of SOLIDWORKS Flow Simulation, R&D engineers validate the release with a suite of 300 tests. NET Framework 2.0 runtime files on target machines. SOLIDWORKS Flow Simulation provides robust verification capabilities for validating designs. This setup package installs Crystal Reports for.
#Solidworks flow simulation fan tutorial cracked
Simulation Download Cracked Average ratng: 3,9/5. The tutorial was originally recorded in 2016 but the basic workflow to get started remains the same.
#Solidworks flow simulation fan tutorial serial number
If you have had SOLIDWORKS installed before, your serial number will.
#Solidworks flow simulation fan tutorial full version
When you create an installer for an application that uses Crystal Reports for Visual Studio, a setup package is made. SolidWorks 2016 Crack Full Version is a best tool which allow you to help ultimate Computer-Aided. In my simulation, my lift is in up direction, so my flow rate must be in down direction. Based on that, i can conclude that if direction of my flow rate is up, my blade lift must be on the opposite direction (down). The Windows Installer allows for smaller deployment projects and reduced installation time. But, the axial flow fan use reaction force of lift to work (3rd newton law).
#Solidworks flow simulation fan tutorial update
If desired, Right Click this folder at any time and choose Update All to effectively re-import and update the project setup from the child level projects.You can use Windows Installer in place of merge modules for deployment projects. Although, I tend to opt for power/efficiency/user friendliness. You dont have a lot of control over the mesh nor any options when it comes to turbulence modeling, but it can get you decent answers for a lot of problems. The imported items will then appear in the Project tree under a folder called From Components. It is fairly limited, but good for conceptual or quick-look analysis. Select the desired project from each subassembly or component, and then choose Add to import these items to the top level. It also contains the computational mesh (except. This will initiate a scan of the assembly which will identify only those components which have projects associated with them. In this blog, I will lay out the different types of SOLIDWORKS Flow Simulation database file types and their function so that you can make storage decisions with confidence.FLD file This file contains the calculation results and is the primary file necessary for saving and loading results. To begin, launch the command from the Tools pull down menu, accessing Tools -> Flow Simulation -> Tools -> Add from Components This includes nearly all setup definitions, including goals. This is the ability to inherit properties from a “child” project – a project defined on a subassembly or component – and bring those properties up to the top level study. Each instance selected now includes boundary conditions identical to those of the original component.Īn additional tool with great time-saving potential is the ability to Add from Components (new in Flow Simulation 2017). Specific instances can be skipped by selectively removing them if desired. This is accomplished simply by creating the initial item of interest (in this case a Fan definition) and then Right Clicking said item, and choosing Copy to Component Instance.Ī dialog then appears and a visual display of all the instances to be copied is provided. This process can be sped up by propagating definitions to other component instances. Setting up Flow Simulation projects can involve repetitive definition of multiple boundary conditions. Save time on project setup in Flow Simulation by utilizing the techniques listed in this blog and companion video – propagating setup definitions across component instances, and importing setup from child components.
